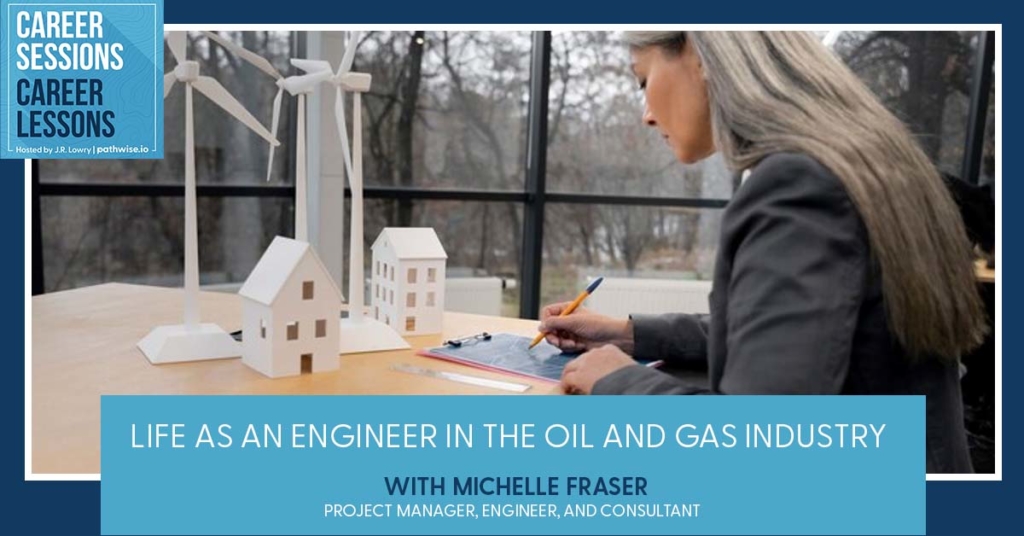
Life As An Engineer In The Oil And Gas Industry, With Michelle Fraser
The energy sector is one of the essential industries in the entire planet. The oil and gas industry keeps the world running, and this is a male-dominated space. Therefore, it is truly remarkable to see women excel and shine here – which is exactly what Michelle Fraser did. In this conversation with J.R. Lowry, the oil and gas commercial and engineering expert breaks down how she interacts with her clients on a daily basis, what it is like to work as an independent consultant, and the systems that ensure safety within their projects. Michelle also talks about environmental sustainability and what it takes to build a world run by renewable energies.
Check out the full series of “Career Sessions, Career Lessons” podcasts here or visit pathwise.io/podcast/. A full written transcript of this episode is also available at https://pathwise.io/podcast/michelle-fraser
—
Watch the episode here
Listen to the podcast here
Life As An Engineer In The Oil And Gas Industry, With Michelle Fraser
Project Manager, Engineer, and Consultant
PathWise is dedicated to helping you be the best professional you can be, providing a mix of career and leadership coaching courses, content, and community. Basic membership is free. Visit PathWise and join. I sat down with Michelle Fraser. She is an oil and gas commercial and engineering expert with over 25 years of global experience in the UK and overseas locations. For the last fifteen years, she has traveled the world managing large-scale projects globally for organizations like Novatek, Total, Yamal, PD&MS, CNR International, and ConocoPhillips. With hands-on experience across multinational, onshore, and offshore locations in the field of plant operations, troubleshooting, and optimization techniques. Michelle has Bachelor’s and Master’s degrees in Engineering and an MBA from Scotland’s Robert Gordon University. She lives in the UK. Michelle, welcome. Thanks for joining me on the show.
Thank you for having me
Let’s start with the work you’re doing. It’s a mix of consulting projects. I gave a brief description in the intro, but fill us in on the kinds of projects that you take on.
I take on a lot of different projects. There are quite a lot of big projects that I’ve been doing lately, managing maybe £5 million to £10 million on projects that are worth a couple of billion pounds. Those are quite a lot of big projects. I have worked in oil and gas and renewables. I’ve worked in all areas of the oil and gas industry and the energy sector.
You got your Bachelor’s degree in Electrical Engineering. How did you end up in the oil and gas industry?
It was quite by accident. I wasn’t going to even start being a technician. I started off as a technician about twelve years ago, but I wasn’t going to be doing that. I was going to be doing something totally different because of how it was many years ago. Women going into male-dominated industries wasn’t a thing that you could do back then. We were already steered towards being the more typically feminine female type of roles, then I got into engineering totally by accident because I decided after school that I didn’t want to follow the normal female type of roles. My mom saw an advert in the paper for junior technicians. I got an interview, and I never looked back from then. I worked in Aberdeen for quite a while. Aberdeen is a predominantly energy sector town. It was natural to go into the oil and gas industry from then.
Do you tend to focus more on upstream projects where the focus is on exploration and production or more on downstream projects where it’s about refining?
I have done both. I have worked in one of the biggest oil refineries at the time over in Shetland. I used to run their metering system. Now it’s mostly upstream.
I would imagine that you’ve been all over the place given that oil exploration tends to happen in the far corners of the world.
I’ve traveled quite a lot. I used to work in Aberdeen and then I’ve worked in Scandinavia. I’ve worked in the Middle East, Malaysia, and all over Europe as well.
I noticed that you speak Norwegian. Did you learn that on the job or did you speak Norwegian before you started working up there?
I learned it on the job because I was there for five years.
What does a typical project look like for you? Who’s bringing you in, if you’re in a consulting capacity, how do you interact with your clients on a day-to-day basis? How long does a project go on? What does success look like?
Usually, agencies bring me in, but because I’m quite well-known in the energy sector, I usually get headhunted by the same company for the last maybe eight years. I’ve worked with them on various different projects. I normally sometimes get headhunted. In the last project that I had, I didn’t even get an interview. Normally, you get a brief interview, but I didn’t get an interview for that one. It was quite surprising. It’s the first time it ever happened.
Basically, what I do is I sit in the client’s office and manage the contractors. I’ve managed various different contractors, all the big ones, the Technique, Saipem, WorleyParsons, which is Worley now, and a couple of other ones. I sit in the contractor’s office and review. It can be anything. I’ve done everything from pre-feed all the way right through to commissioning and hookup to handover. I can be doing various different types of roles in different projects. I could run the project from start to finish.
What is success to me? It’s being able to fix all the difficult problems that a lot of people can’t. I think that’s what I look to have, complete what I’ve been taken on to do and the time skill that I’ve been taken on to do it, which could be quite a lot of different things. In this project that I was finishing now, I was able to work on cybersecurity, which is one of the first times that I’ve done that as well, which is a major thing now in the whole of the oil industry. Normally, cybersecurity would be something that maybe the Middle East would do before, but now it’s been called on even across Europe as well.
Success is about being able to fix difficult problems that a lot of people cannot. Share on XThe threats are certainly there. It’s there in any industry. You have systems that are managing something potentially deadly as oil production. You certainly want to make sure that a bad actor can’t get in and adjust things in a way that ends up harming safety or harming production in some other way. What’s it like being on an oil platform day-to-day?
I like being offshore. Offshore is good. Sometimes the flights are not that good. I like being offshore, not all the time, but I only go off once in a while. For me, it’s the only way that you can have an appreciation for what you are working with is to see inspiration and to see what you’re building, to see how it works. You’re not going to be able to do that. You can write about it and design it and read about it a lot in the office, but until you go offshore or on-site, you’re not going to be able to have an appreciation about what you’re doing.
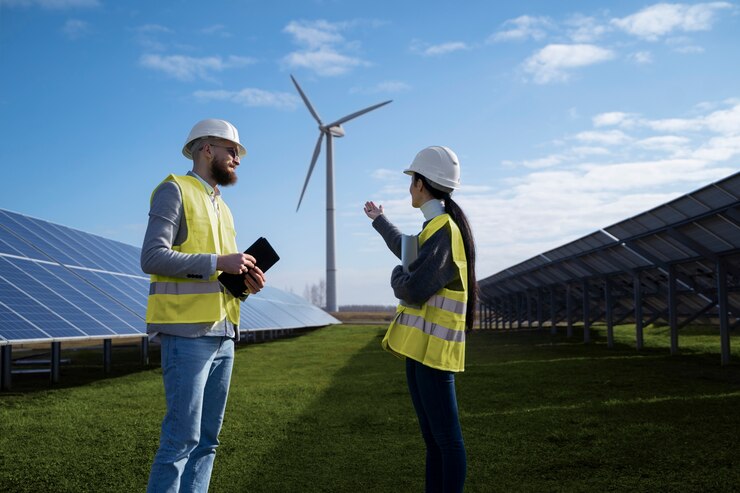
Michelle Fraser: The only way to fully appreciate what you are working on in the oil and gas industry is to visit project sites personally. You cannot just write or read about it in the office.
When you go out, how long are you typically out there at a stretch?
One week, but being on-site, I used to do 8 or 10 weeks away and 2 weeks back. I was in China when I was on-site at the big L&G plant. I like that.
I would imagine whether you’re in a plant that’s far from home or on an offshore platform, there’s an intensity of the experience and focus that you get to be working on your craft. You go to an office every day and you drive in and you drive home and you let it go every day. You create distance between work and home. It’s not quite the same as living and working on an oil platform or at a plant for a period of time.
It’s not. Being an office is quite all right if that’s all you want to do. I would advise any young person coming into the industry to try and go offshore or on-site only for a couple of weeks and you only do it once. It’s exciting and then you get to see what you’re working on and all the problems that could arise. Even what you’re designing on being on-site when it was construction, even your initial concept during pre-feed and feed to going into installation, what you have down on paper at the very beginning, even about maybe 2 or 3 years ago might not even work when you’re on site. You have to do problem-solving.
There is that stigma that maybe some site engineers are also good, “I’m going to try put my neck out and say that,” but it’s not even the case. The site engineers are extremely clever people because they have to troubleshoot. Every time you stop production or construction to fix a problem, it costs a lot of money. You have to keep things going. You have to think on your feet and get the problems resolved before it goes offshore because on-site, you can get a lot of people on the platform or the plant. Whereas when it goes to the final destination or offshore, you’re limited to bed space and everything like that. It takes longer and it’s much harder to fix a problem.
You’ve mentioned pre-feed and feed a few times. For me and the audience who are not familiar with some of the industry jargon, what stage of the process are you referring to there?
Pre-feed, you have an initial concept which normally runs about 4 to 6 months, then you have pre-feed, which will run about 6 or 7 months at the most or maybe 1 year. It depends on how well it goes. Pre-feed is when you take the initial concept and you develop it further to a cost. You have feed, which is where you develop the design a lot more then you go into detailed design and then it’s construction, then pre-commissioning and commissioning, then it’s mechanical completion. There are a lot of different stages and projects until you get handover.
Did handover mean when production starts?
No, handing over the systems to make sure that the systems work as they’re supposed to. That’s what I was doing in this last project. When I was working on the ICSS system, which is the Integrated Control and Safety System for the platform. I was also handing over the RCR, which is a Remote Control Room.
What are some of the ways that you specifically help to improve safety and operations? That has to be paramount.
You have your ICSS system that controls a lot of the platform safety. It’s quite a crucial system, then you have your oil and gas, cybersecurity, ESD, emergency shutdown system, and PSD. You have a lot of these systems going on and about to keep everything safe.
I would imagine there are parts of this that are well-developed and industry standard and parts of this that are very specific to the site, what you’re pulling out of the ground, and other things as well. Is that the case or is it mostly pretty standard at this point?
It’s mostly pretty standard. You’re pulling out of the grind, whether it’s oil or whether it’s gas, but the systems to keep everything safe, like your cybersecurity and ICSS system. It’s developing all the time. Technology is developing all the time. Typically an ICSS system will only last you maybe about 5 to 10 years before it becomes obsolete.
At that point, you would want to put in something new to make sure you have the latest and greatest available.
Yeah, because they stop making parts after about maybe five years at the most.
There’s a lot of focus on environmental sustainability. How does that factor into the kinds of things that you do?
It’s a big issue, sustainability, although some people say that they don’t think the oil industry is going to be sustainable. There is a clear focus all over the oil industry on sustainability and net zero and to work on that. It’s not going to happen overnight. I don’t think that there’s going to be a magic switch that’s going to turn it off in maybe about 5 to 10 years. I don’t think you’re still going to need the oil industry going forward.
There is no magic switch in sustainability. It cannot happen overnight. However, there is still some need for the oil industry moving forward and cannot be eliminated completely. Share on XYou hear all these different viewpoints on that topic. People pushing that we should go all-electric or alter renewables. The cost that is required to make that switchover is not going to happen overnight.
I don’t even know if you have the infrastructure and technology in place to have it happen overnight. It takes quite a long time for it to be all-electric or all. I don’t even know if it would happen at some point.
At some point, I imagine it will, but not probably for a long time. That’s hence the challenge I think that a lot of people feel with respect to environmental impact. You mentioned at the outset being hesitant to go into a male-dominated industry. How has it progressed in the time of your career? Do you still feel like you have to work extra hard to prove yourself because you’re a woman or has it gotten more even footing over the years?
I think it’s worse than it’s ever been, especially with the younger generation coming in, I would think that it’ll get better slightly, but I don’t think it’ll ever change. I think it’ll be how it is. As a female engineer, I would always feel like I have to strive to prove myself all the time to the project that I go to.
It’s got to be a grind.
It’s hard work because you have to think about it if you’re a contractor consultant and the client wants results quickly.
I would imagine, there is a bit of arm’s length in that relationship when you’re a contractor or a consultant. It’s not like you are an employee and when you’re working in that capacity. There’s always a little bit more of you coming in and proving yourself in general because you may be new to the organization even if you’ve got a reputation that you do.
I always feel like I have to try and prove myself all the time, try and keep up the hard work, and stuff like that.
You’ve worked your twenty-ish years or whatever into your career at this point. How much of that have you spent working in a contractor consultant capacity and how much of it have you worked as an employee?
I’ve not worked as an employee since 2006.
What is it about working as an independent consultant that appeals to you?
It doesn’t matter now. I think it’s okay as long as you can get the consistency of work all the time because you hear that some contractors are maybe sitting at home for about six or so months and that can be tough. If you can get consistency in work, which can be quite hard to do, then it’s okay, but I like being a contractor. It’s a lot more money. I think that’s what a lot of people find attractive about it. It can be quite a lot more money. It gives you the freedom as well.
You can do more traveling. You can go and work for different companies as well, even though I’ve worked for the same one pretty consistently for the last eight years. You could go off. I think it does give you more freedom. You get to come in and do a specific piece of work. I think if you were maybe staff, you would have your normal general role every single day. Whereas if you’re a contractor, you get to do a lot of different types of work that maybe a staff person can’t do or they maybe don’t want to do so you get more difficult problems to solve as well.
It sounds like you don’t have to work overly hard at this point to generate work that you’ve got enough of a reputation and demand. You’ve been working for Total for the last eight years. There’s some steadiness in it, even if you’re working in a contract capacity.
I’ve been quite lucky. You have to take the downside with the upside though. It’s not always been pretty consistent. Sometimes there have been some low points but it is what it is when you’re a contractor.
There are low points when you’re an employee too.
I think so as well.
What do you do during downtimes if you have downtime?
I have my podcast now. I started my own podcast, Energy Sector Heroes. I do that in my downtime and also my spare time as well. It’s not too hard work to keep it going, but I enjoy doing it as well. You get to meet a lot of amazingly interesting people.
How long have you been doing your podcast?
Nearly a year in January.
How often do you do new episodes?
I do it once a week. I love doing it.
I would imagine you learn a lot about other parts of the industry that maybe you haven’t had as much exposure to by talking to people who are working in different areas of the industry.
It’s interesting to hear about people’s different stories as well. My podcast is about storytelling and hearing about other people’s careers, but it can also be going to technical discussion. It can be quite exciting.
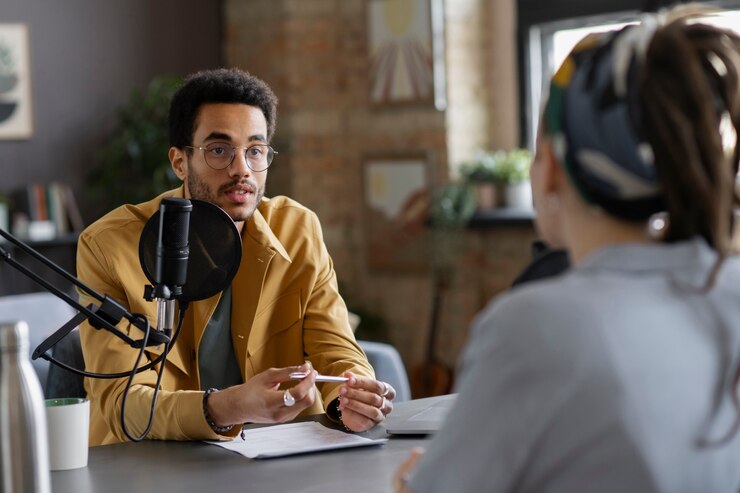
Michelle Fraser: A podcast is not just about storytelling or hearing about other people’s careers. It can also be a technical discussion.
We won’t do a technical discussion here. It would last about a half second and you would run over me based on my relatively limited knowledge of the oil industry. Talk a little bit about your day-to-day.
My day usually starts early. I have to be in the office maybe about 7:30 and then we have a morning meeting with offshore to make sure that everything’s okay and if there are any problems overnight or from the previous day, then we have to go and resolve them. I would normally have a couple of meetings. I would normally have to work on orders. In the last job I had, I had to do some work orders from technical issues with the equipment that wasn’t working. I would also have to get the maintenance routines prepared, but then you also get to do more interesting things. I had to look after some of the cybersecurity systems as well and implement a strategy about how we’re going to upgrade and maintain it.
Do you have a time in the day when you feel like you’re especially productive?
Probably, in the morning,
It sounds like you get thrown right into those morning meetings. You don’t necessarily have that time for yourself.
That’s why I like to get in quite early.
How do you like to start your day? What do you like to do to get yourself ready for the day?
I usually walk to work. I live and try and get an apartment quite close to work so I can walk to work.
This is a high-stake industry and environment. How do you deal with the pressures that come with the role?
I do like the pressure. I thrive under pressure because it’s a fast-paced industry and the roles that I have is quite fast-paced. Your bosses want results quite quickly. You are under pressure nearly all the time.
These are expensive projects to set up. They’re expensive operations to run. Once they get running, every minute counts literally. How do you balance the pressure to keep things operating or to keep yourself on schedule in terms of getting production up and running versus the risk of safety issues?
Safety always comes first because you have to realize that the men and females that are offshore have families to go home to. Safety is quite an important issue. You have to work to the standards. We have standards and procedures that you have to adhere to make sure that you are not compromising safety issues when you’re doing your day-to-day work.
Safety always comes first in the oil and gas industry. Everyone has their own families to go home to. Share on XDoes the industry do a good job of encouraging people to speak up and voice concerns or do you still find that there are certain situations where people are afraid to raise those safety concerns or whatever concerns?
It’s not how it used to be many years before. It was like that. People might have been frowned upon for raising safety issues, but it’s not even like that now. It’s more open and welcoming. You’re rewarded now if you find any major issues. It’s not like it was before. It’s moved a lot further ahead in that instance. Safety is always at the forefront.
How do you keep boundaries set up between work and personal life so that you have a good balance?
It was quite hard before because if you’re away, it’ll hang about together. I do hang about with them. I do go out with them quite a lot. Since I started my podcast, I’ve had other things to concentrate on, which I find a lot beneficial to myself.
Do you mean in terms of doing your podcast or other things besides the podcast?
I do a lot of exercise as well. For me, you can’t always be working together and out together. It is nice, but not all the time.
When you’re off and you’re working on those projects, and you’re someplace away from home and everybody’s away from home, it is a fairly full-on experience. Those can go well or not well, depending on the dynamics of the team. There’s often pressure for everybody to be together and I would imagine that’s hard at times.
I’m quite lucky that I have a lot of outside activities that I do. Although we do great together quite a lot as well.
You spend a lot of time working in a setting that’s very different from a traditional office. How has that shaped your view of what leadership is?
A good leader should be approachable with effective communication and empathy. For me, being able to help the people offshore and on-site if they need any help, you would need to make yourself available to them.
It goes back to what we were talking about in terms of creating an environment where people can feel heard. As a leader, it’s especially important in those stake situations that you have a sense of being even-keeled, not overreacting to a piece of news, and all of those things that in an office setting, where it isn’t a life and death situation, you could probably get away a little bit more with, I’ll say some bad behavior as a leader, but bad behavior in a leader in a high stake situation where safety is paramount can get people killed or hurt if the leader is not in the right mental space.
Everybody has problems in the background, but I think you need to try to not bring that to work. It is easier said than done. It depends on how you define a bad leader. There are different styles of leadership and maybe my style of management and leadership might be different to someone else’s. I wouldn’t say that mine is the right way and theirs is the wrong way. I think everybody has different ways of working.
How would you describe your own leadership style?
Hopefully, I would have a lot of empathy. I was approachable. Being able to listen and help people try to resolve problems as quickly as they could.
Is there anybody that you think of as a leader that you’ve particularly admired, either somebody that you’ve worked with or somebody perhaps more from a distance?
There are a couple of people. One is my previous boss, which was Bruno Peek. He was a good leader. I worked for him three times. I liked him as a leader. He was quite strict but quite fair. He was running a major project running several billion pounds. He was a good leader. I liked him. My other favorite leader was Ray Hillard. He taught me a lot and gave me a lot of responsibility for the project that I had. He gave me a lot of confidence when maybe I didn’t have that much back then, which I will always be internally grateful for. He’s a good and nice guy.
What did he do to help you build your confidence?
He gave me a lot of responsibility. He was my engineering manager at the time. He let me do a lot of his work. I did it quite confidently and quite competently. He did say to me at the end of that contract, “You can do it. I would make an amazing leader.” It’s always stuck with me as well.
I think when you have a leader that pushes you a bit outside of your comfort zone, it may be a little bit intimidating at the time, but that’s how you grow. What he gave you was that opportunity. When you look back, you’re midway into your career, on the career decisions that you’ve made, how much of it would you say you’ve been intentional about and how much would you say that you’ve been opportunistic about?
I don’t know. I thought about this before. I’ve never had a five-year plan. I don’t think I’ve intentionally chosen projects I work to do. I think I have chosen the ones that I work to do because sometimes when I get contacted, I don’t even get a job description. They tell me to come and then I find out what I’m doing when I start challenging as well. Most of the time I don’t know what I’ll be doing until I get there. I’ve had that quite a lot of times. It’s mostly being opportunist. Sometimes like the blue.
It sounds like it, but it also sounds like you go back to your point about competence, to go into a situation where you’re not even exactly sure what you’re going to be doing or perhaps what success means in that project. You have to be confident in your ability to come in, figure it out, and get the job done.
I always worry before I start something or a new contract, “What am I going to be able to do? What am I going to be doing? Are they going to think I’m going to be doing a good job?” Everybody thinks that. Even 30 years on, I still get that. It’s like a nervous energy because everything works out in the end and you’re worrying about nothing.
There’s that difference between excitement which has more of a positive connotation, and anxiety which has more of a negative connotation, but they’re both nervous energy in one form or the other. It sounds like you’ve figured out how to channel that into excitement rather than anxiety.
Yes, because I’ve been used to doing it. I’ve been doing that for quite a while now.
What are the strengths that you’ve drawn on over the years that have helped you to be successful?
I think consistency and persistence because you have to be persistent. Sometimes the problem that I have to resolve, you could be working on it for months because it could be one thing and then you go down one avenue and then it might not even be that, then it might be something different. You’re always trying to figure out how to troubleshoot a problem that could be quite difficult.
That might take quite a long time to resolve. You have to have the persistence to keep going when you meet a brick wall. Maybe have to go and talk to someone else to try and get some more information about, “How we’re going to resolve this problem?” It’s not going to go away. You might hope it might go away, but it’s not going to go away. It’s still going to be there and you’re still going to have to fix it.
When you’re in the midst of doing an implementation project, a new facility, or a new offshore platform, if you don’t solve the problem, then the work doesn’t go ahead. It’s a bunch of money wasted. You have to solve them. It’s not a game that you can walk away from or a puzzle that you can walk away from. You have to enjoy that give and take that happens in being a problem solver because sometimes the solutions don’t reveal themselves as quickly or easily as you would like.
Sometimes I’ve worked on one problem that has maybe taken me quite a few months to resolve. I could have inherited that problem from someone else who probably already started. It got sidetracked. Maybe figure out how to go forward with it. They’ve handed it over to me on starting the contract. I’ve had a lot of problems that I’ve inherited then I’ve had to try and troubleshoot. It’s then taken me quite a few months after somebody else has been working on it for quite a few months as well. It’s the way, but you have to be pretty persistent to keep it going.
If persistency and consistency are strengths. What are some of the things that you’ve had to work on developing over the years?
Effective communication. I was quite shy but since starting my podcast, it changed me quite a lot. The hardest thing that you have to work on and it’s new. You’re almost in a losing battle every day because in every project that you work on, even though it’s with the same company, it’s always different people. You always have to find out everybody in the project who could be useful to you. You have to find out who they are, what their name is, how you contact them, and stuff like that because they could save you a lot of time. You would have to have quite good investigation skills and probably good communication skills to drive a problem forward
When you’re constantly stepping into a new situation with new people and trying to figure out, “What’s been done, what hasn’t been done, what’s been thought about, what hasn’t been thought about, where do I pick this up and push forward,” that’s a skill in and of itself.
You can almost say if you’re a contractor you’re starting a new job in a new company every 1 or 2 years, which is stressful enough because some people don’t change jobs 5 or 7 years and you’re doing it quite consistently. It could be stressful enough doing that, then you’re having to learn all these new people.
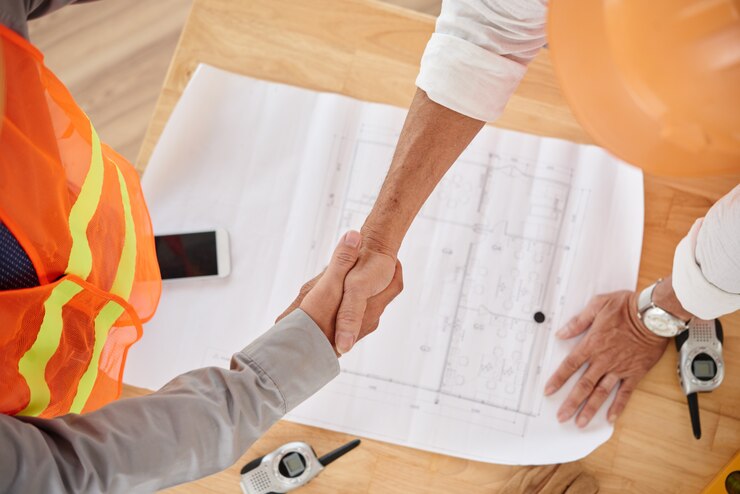
Michelle Fraser: Contractors start a new job every couple of years. It is stressful enough and must be approached with a certain level of consistency.
What has been a big challenge that you faced along the way and how did you work to overcome it?
The biggest challenge I’ve had to face is being accepted by males in the industry. I have to work hard to prove myself.
It’s got to be frustrating. It wasn’t an even playing field and you probably watch your male colleagues not having to work that hard to establish credibility and that can’t feel fair.
It is what it is. You have to accept it. I don’t think it’s going to change anytime soon. I hope it does.
What do you wish somebody had told you at the beginning of your career that you know now?
Worry less.
I hear that a lot.
I worry less because it’s never going to happen. I only worry about it when it happens. If I could change anything, I wish I worry less.
Any final advice you want to offer our audience?
Come to the energy sector, even as an engineer or maybe not as an engineer. It’s an exciting place to be, full of challenges and opportunities.
We need the industry. It’s essential to our day-to-day functioning as a society. We need people going to it. We need people bringing new ideas to it. That was part of my reason for wanting to interview you, to bring it to the forefront because it’s an important part of our economy.
I wholeheartedly agree with that as well. I don’t think it’s going to be going away overnight.
Thanks for doing this. I appreciate your time.
Thank you for having me. I appreciate it. I have a lot of fun as well.
Have a good rest of your day.
You too.
—
I’d like to thank Michelle for joining me to cover her work as an oil and gas engineer and some of the lessons that she’s learned thus far in her career. If you’d like to make the most of your career, visit PathWise.io and become a member. Basic membership is free. You can also sign up on the website for the PathWise Newsletter. Follow us on LinkedIn, Facebook, YouTube, Instagram and TikTok. Thanks. Have a great day.
Important Links
- Michelle Fraser
- Energy Sector Heroes
- LinkedIn – PathWise
- Facebook – PathWise
- YouTube – PathWise
- Instagram – PathWise
- TikTok – PathWise
About Michelle Fraser
Michelle Fraser is an oil and gas commercial and engineering expert with over 25 years global experience in the UK and overseas locations. For the last 15 years, she has travelled the world managing large-scale projects globally for organizations like Novatek, Total, Yamal, PD&MS, CNR International, and Conoco Philips, with hands on experience across multinational onshore and offshore locations in the field of plant operations, troubleshooting and optimization techniques.
Michelle has Bachelor’s and Master’s degrees in Engineering and an MBA from Scotland’s Robert Gordon University, and she lives in the UK.